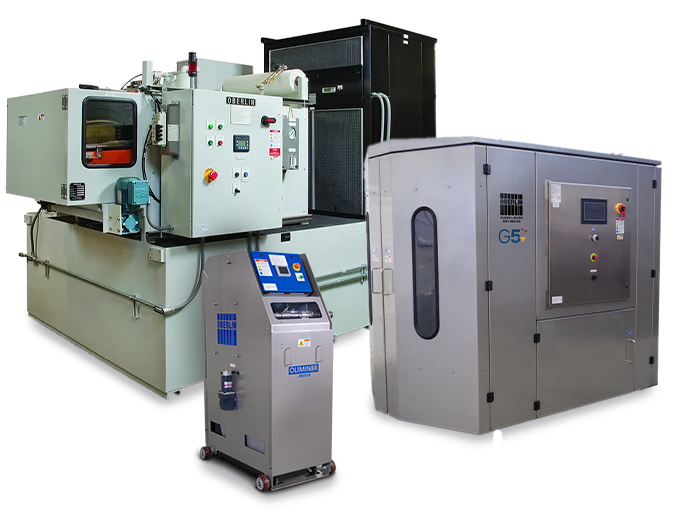
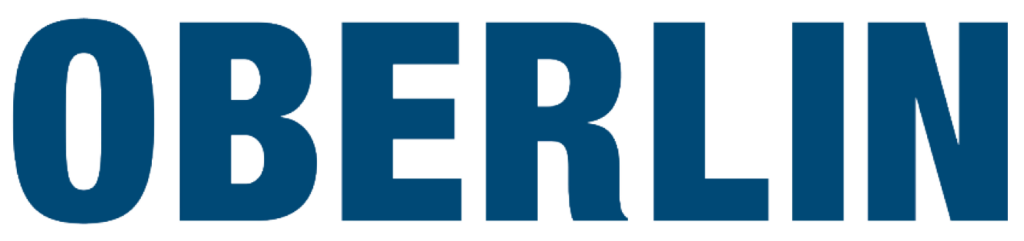
Start Your Journey Towards Better Filtration.
Good Businesses Waste Money on outdated Filtration Systems
Turn Your WASTE into SAVINGS. Why wait?
ENGINEERING MANAGER
president
vice president
See Why Leading Companies Choose Oberlin Filters
1. FILTERING CYCLE
The pneumatic actuator moves the filter chamber (platen) into position, and holds it against the other chamber. Platen seals on the perimeter of the chamber create a liquid-tight seal around the filter media (disposable or semi-permanent belt). Solids-bearing liquid is pumped into the upper chamber, where the solids are trapped by the filter media. Pump pressure continues to force the liquid through the filter media and the previously collected solids.
2. DRYING CYCLE
When the pressure inside the filtering chamber reaches 30-40 psi, compressed air or other inert gas is fed into the upper chamber. This forces the remaining liquid in the chamber through the trapped solids and filter media. After all the liquid is evacuated, the cake is further dried using the compressed air. Once the drying cycle is complete, determined by backpressure and elapsed time – the chamber is lifted.
3. DISCHARGE CYCLE
Once the chamber is lifted, the solids (filter cake) are automatically discharged by advancing the filter media one section. After discharge, the upper chamber descends and a new filtering cycle begins. This sequence continues automatically until ended manually or via electrical signal.
OBERLIN PRESSURE FILTERS
Applications Unlimited
Watch An Oberlin Filter Perform LIVE
elevate your performance
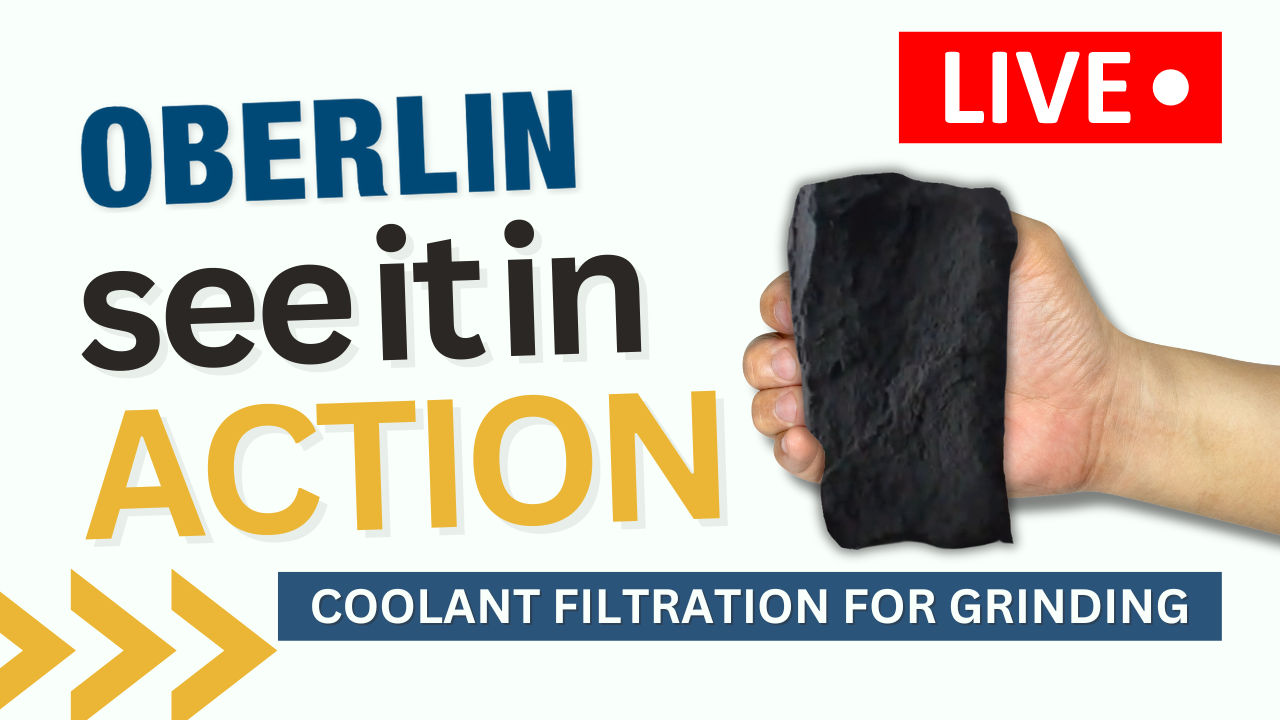
keep exploring
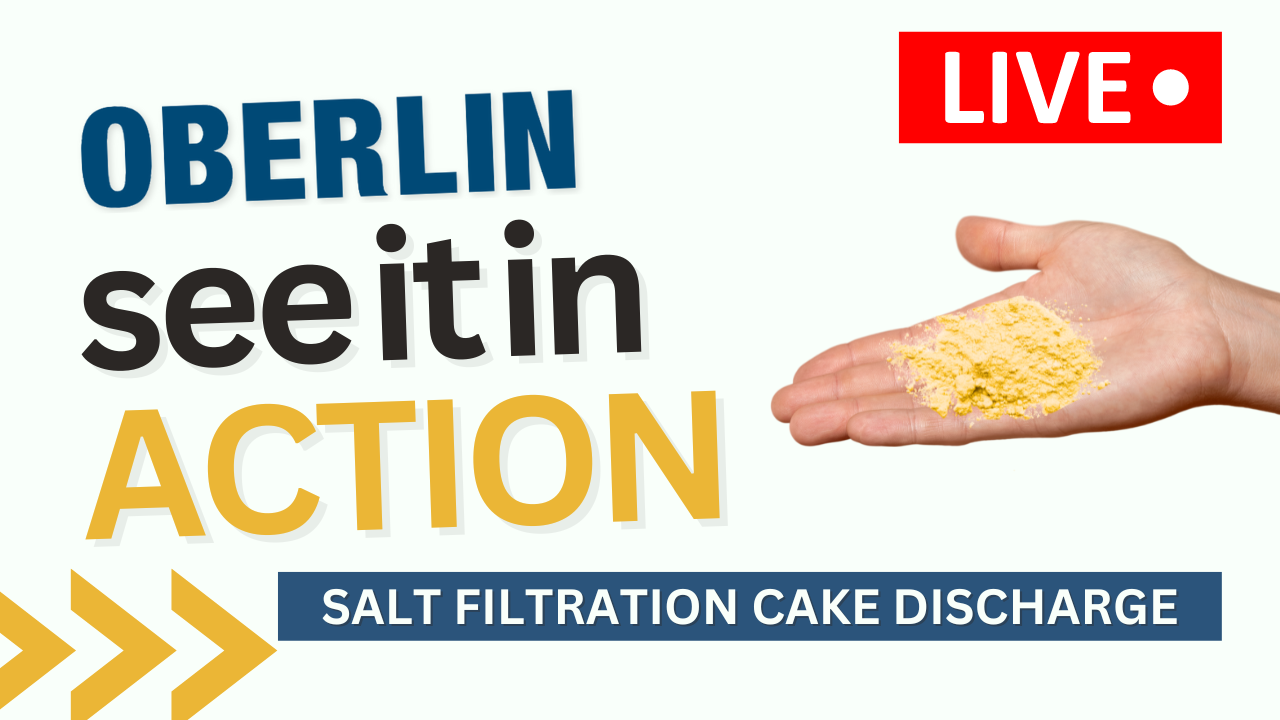
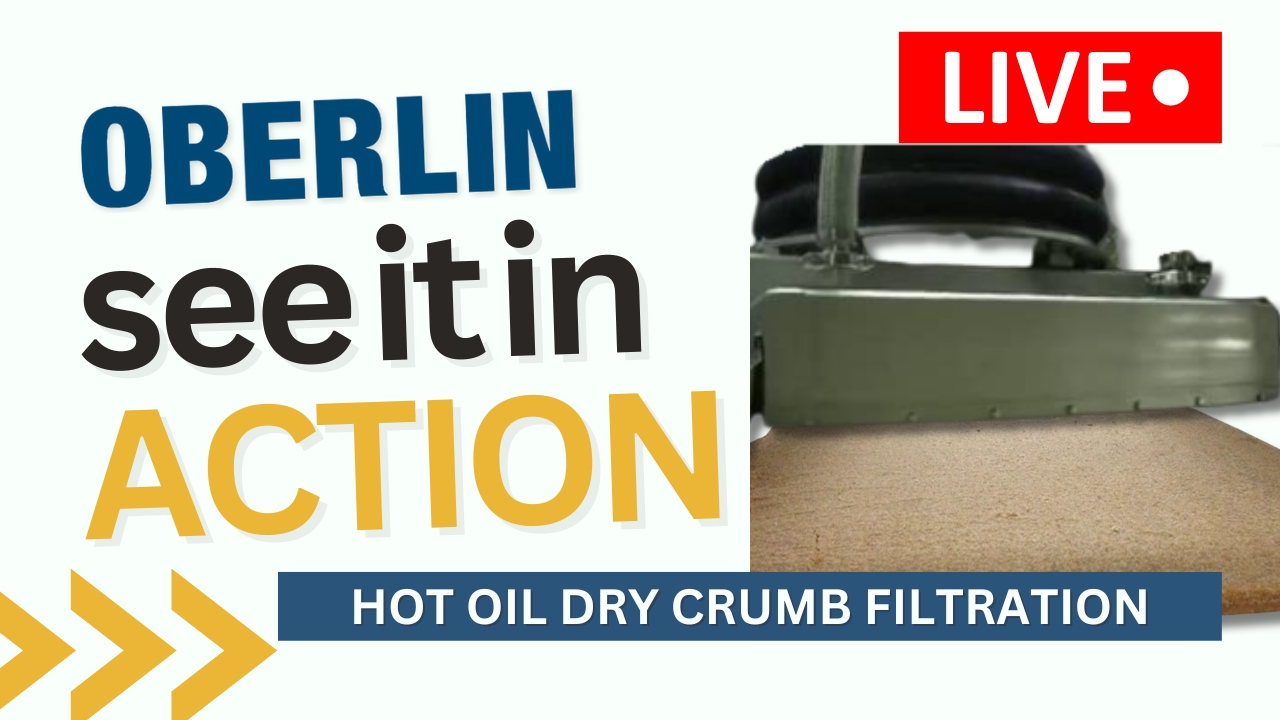
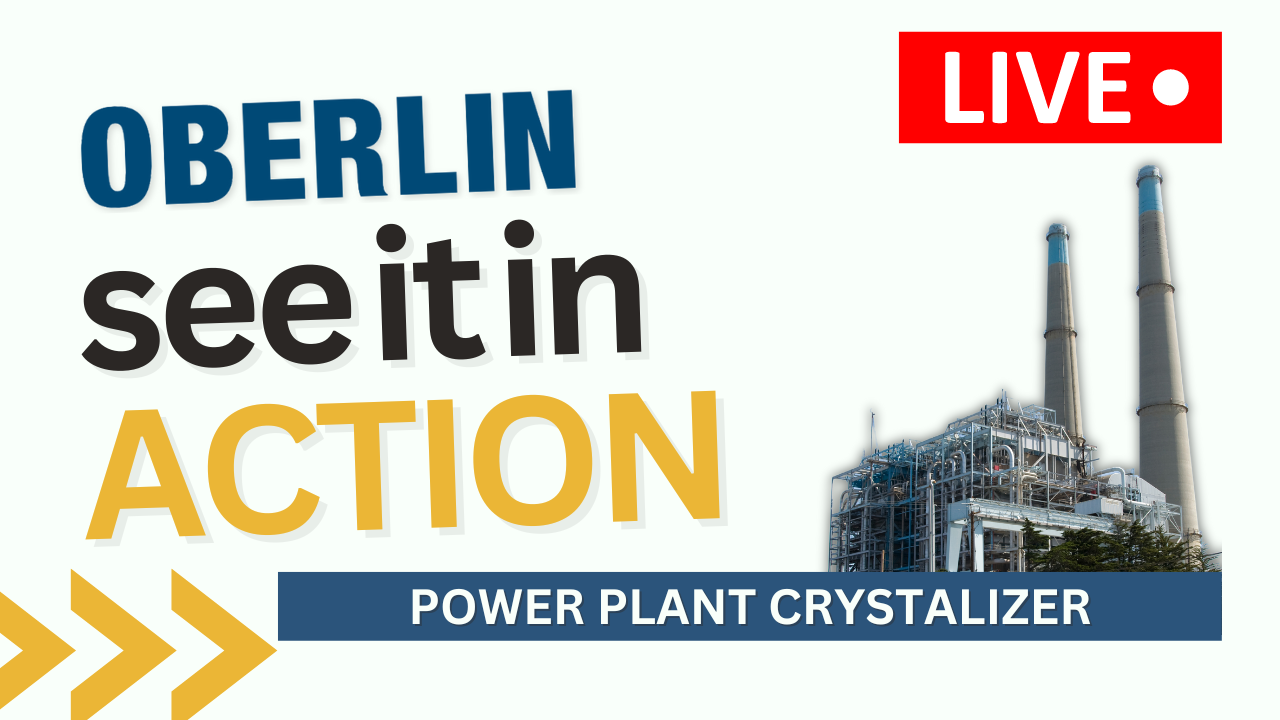
Where in the World is An Oberlin Filter?
Displaying Approximate Location / May Not Reflect All Locations
Let's Talk Solutions.
Connect with a Trusted Filtration Expert.
“The Oberlin Automatic Pressure Filter(APF) is unique in the industry since it’s simple, automatic, and can use disposable filter media for the same capacity cycle after cycle. It can be manufactured from many materials of construction to meet the most corrosive environments. It can also handle almost any solids loading and can accommodate in-line filter aid or polymer flocculant addition for enhanced separation efficiency. These are some of the reasons that more than 60 units have been installed in DuPont on a variety of applications including wastewater, recycle water clarification. nuclear waste treatment, and metals recovery.”
dr. ernest m. | senior consultant