SINGLE CNC MACHINE COOLANT FILTRATION
Any Fluid – Any Material | Individual Machine
Increase CNC Machine Uptime and Save Thousands Annually!
The OLIMIN8R is an automatic pressure filter that removes the chips and fines that bypass the machine tool chip conveyor during the CNC Machining process. It can be connected to any existing CNC Machine sump with a tank height of 27” or less and coolant volume up to 400 gallons. The OLIMIN8R captures the dirty coolant as it exits the machine tool chip conveyor, removes the solids and delivers the clean coolant where most important – near the clean machine tool coolant pumps.
It removes the chips and fines before they have a chance to settle onto the bottom of the CNC Machine sump, preventing the larger solids from piling up in the machine sump – creating a chip dam. This reduces sump clean outs and eliminates coolant overflow and coolant foaming due to pump starvation.
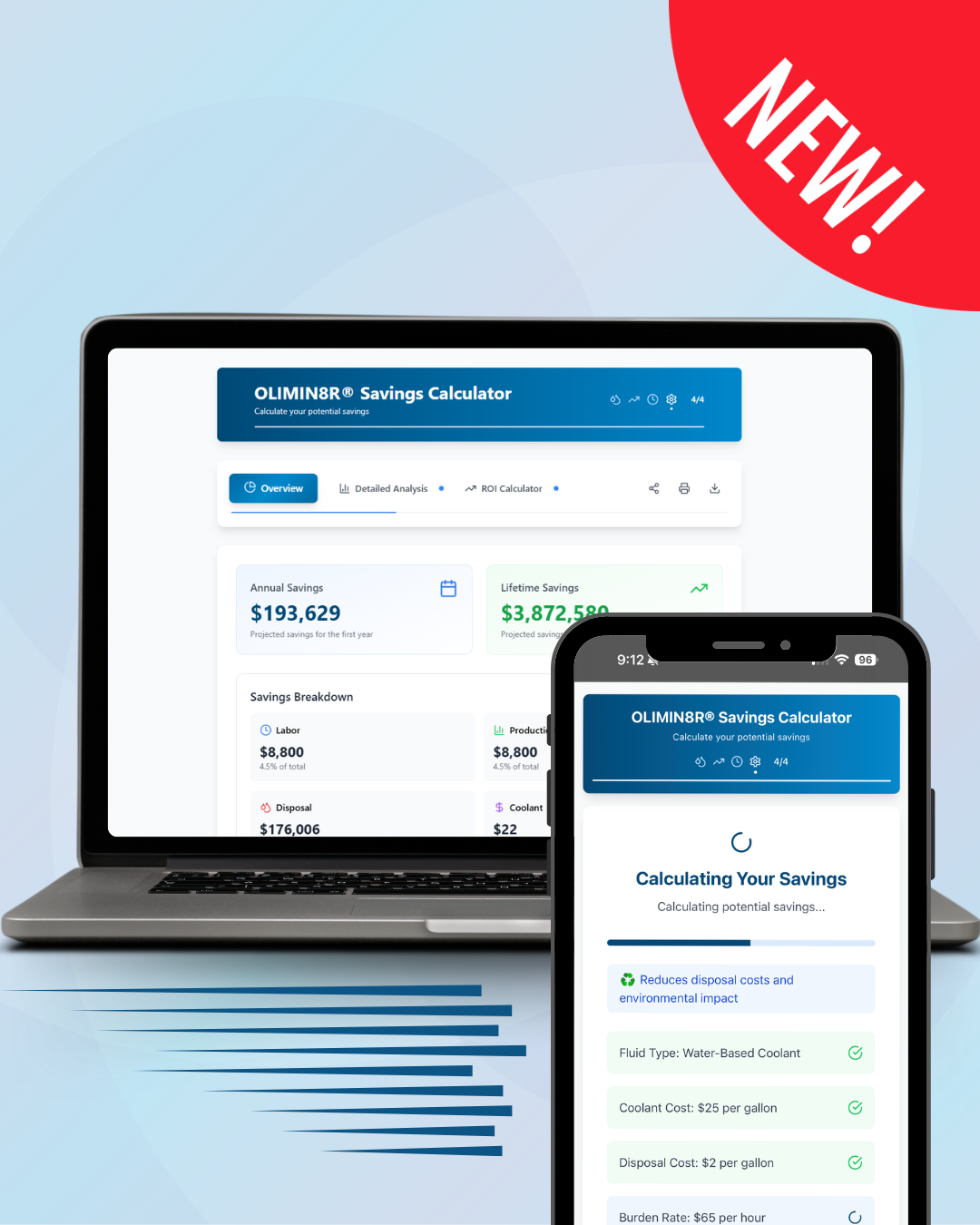
CALCULATE YOUR ROI & ESTIMATE IN 90 SECONDS!
Stop wasting time and money on clogged CNCs! Increase CNC Machine Uptime and Save Thousands Annually! The Oberlin OLIMIN8R automatically filters coolant, extending machine life, saving you thousands on maintenance and downtime.
How the OLIMIN8R Works
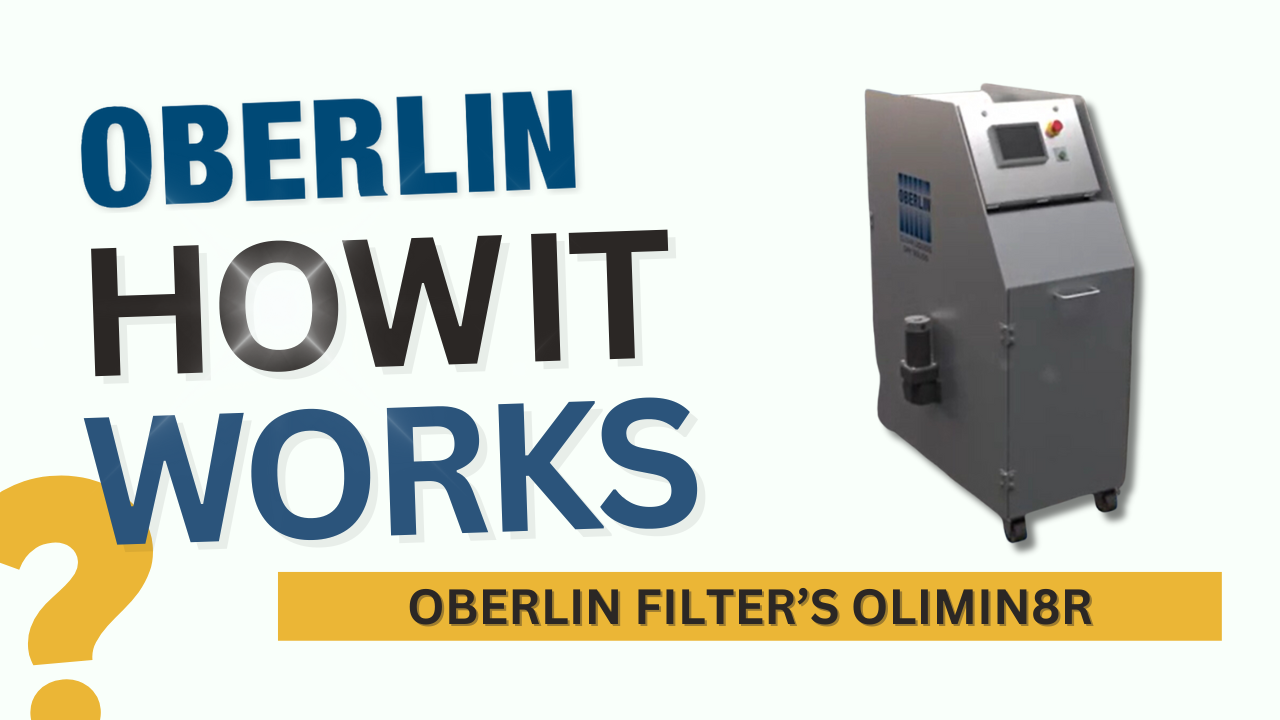
More Benefits of CNC Sump Filtration with The OLIMIN8R
The OLIMIN8R removes the fine solids that plug coolant ports and shut down your CNC Machine. The OLIMIN8R can greatly increase machine uptime providing great savings. You’re not making parts or money while your CNC machine is down for cleaning. For every hour spent moving machine tool chip conveyor belts, shoveling out machine sumps and cleaning coolant ports, you’re losing production time that can translate into hundreds, maybe even thousands of dollars.
The OLIMIN8R will provide increased production time and prolonged tool life. It greatly extends the life of the coolant so it doesn’t have to be discarded prematurely – greatly reducing waste disposal costs and labor hours. The OLIMIN8R turns dirty coolant into clean coolant and leaves you with only the dry solids to dispose of.
Common Problems Eliminated with Advanced Filtration
Problem | Status |
---|---|
Frequent Sump Cleaning | ✓ REDUCED |
Coolant Port Plugging | ✓ ELIMINATED |
Chip Dam / Coolant Overflow | ✓ ELIMINATED |
Chip Dam / Coolant Foaming | ✓ ELIMINATED |
Plugged Pump Screen / Coolant Foaming | ✓ ELIMINATED |
Plugged Drum Screen / Coolant Foaming | ✓ ELIMINATED |
Coolant Filtration for Many Machining Applications and Materials
Coolant Types
- Water-Soluble
- Semi-Synthetic
- Full Synthetic
- Straight oils
APPLICATIONS
- Broaching
- Drilling
- Hobbing
- Milling
- Turning
MATERIALS
- Aluminum
- Carbide
- Carbon Fiber
- Cast Iron
- Stainless Steel
- Steel
CASE STUDIES & TESTIMONIALS
Testimonial
“We were in a position where our machining process was not keeping up with production demands due to clogged tooling. We incurred over 1,000 hours of down time/lost production and $60K in additional costs due to indirect labor for increased coolant tank cleanings, filter changes at every shift change, operators trying to clean clogged tooling and increased tool changes. We also tried Magnetic filters and Twin bag filters with an external pump with no luck. I reached out to Brian Pfau at Oberlin; he presented us with an option to trial the new OLMINI8R. The results were immediate; the tools did not clog, per shift filter changes went away due to a roll of filter paper in the OLIMINI8R last 2-3 months and tank cleanings went from every 30 days to 180 days. Even our Operators are impressed with how easy the controls are to use and maintain. I am the Maintenance Supervisor at Weasler Engineering and the OLIMIN8R has significantly improved our operations, saved us time and money and improved overall employee morale.”
Forrest Koenig
Maintenance Supervisor
CASE HISTORY: Large Manufacturer of Power Transmission Components
Ductile & black iron machining, water-based coolant:
Prior to installing the Oberlin Filter this company was cleaning coolant ports every shift and pulling the sump for cleaning every three (3) weeks. In fact, the tool plugging was so bad that the tools were periodically ejected from the tool holder, thereby damaging the tooling. Management couldn’t find an operator willing to run this machine as one of their responsibilities was cleaning the ports.
With the Oberlin filter the coolant port cleaning was eliminated entirely and the sump cleaning frequency was extended beyond the 6 month normal cleaning frequency for all other machines.
CASE HISTORY: Large Manufacturer of Marine Engines
Steel turning and hobbing, water-based coolant:
Prior to installing the Oberlin Filter this company was pulling and cleaning the coolant sump every 1-2 months. The main problem was coolant foaming due to small chips and fines piling up in the machine sump. The buildup reduced the coolant volume in the sump and prevented coolant from getting to the clean pumps, thereby promoting coolant foaming. This customer was also experiencing coolant port plugging but this was not the main driver for the filter.
CASE HISTORY: Large Manufacturer of Small Engines
Cast iron drilling, water-based coolant:
Prior to installing the Oberlin Filter this company would experience coolant overflowing from the sump tank every 10-12 weeks due to fines building up in the machine sump (chip damming). Their goal was 24 weeks of coolant life. With the Oberlin Filter they were able to run the machine to 24 weeks with no coolant overflows.
CASE HISTORY: Large Aluminum Die Cast Company
Aluminum machining, water-based coolant:
Prior to installing the Oberlin Filter this company would experience frequent low coolant pressure alarms at the machine. These were due to aluminum fines piling up around the clean pump suctions (chip damming). This company has no regular maintenance interval and only cleans out the sumps if they absolutely have to. After the Oberlin Filter was installed the machine experienced no low coolant pressure alarms.
CASE HISTORY: Large Medical Imaging Company
Graphite machining, water-based coolant:
Prior to installing the Oberlin Filter this company would experience frequent machine sump clean outs and was experiencing surface finish issues due to the high level of fines in the coolant. After the Oberlin Filter was installed the dirt load in the coolant remained at or below 5mg/L @ 5 micron for the entire month. This eliminated both problems.